A growing wave of grassroots legislative action is reshaping the landscape industry as municipalities nationwide implement increasingly stringent regulations on gas-powered equipment. While often framed as noise ordinances, these restrictions are sometimes driven by a desire to eliminate gas-powered tools, with noise complaints serving as the Trojan horse. Now, landscape professionals face the complex challenge of navigating local restrictions while providing clients with quality service.
Landscape industry pros and insiders offer five strategies and best practices to better serve clients while adhering to these restrictions.
Stay involved and informed
Direct and consistent engagement with local government is crucial for landscape professionals navigating these evolving regulations, says Kris Kiser, president and CEO of the Outdoor Power Equipment Institute (OPEI). To stay on top of the issues municipal councils are dealing with, Kiser advises contractors to stay on top of meeting notices, proposed ordinances and meeting agendas, all accessible online or through the local media.
“You need to be aware of what’s going on in the communities you’re working in and recognize, as a business, that if these (restrictive ordinances) are going on the books, it’s likely a result of a complaint or group of complaints,” Kiser says.
Operating in a distinct geographic area, and often being residents themselves, gives contractors and their crews a specific advantage about the political climate of the communities they serve, says Bob Mann, NALP’s senior director of technical and regulatory affairs. However, this familiarity should not supplant proactive due diligence.
“If you don’t understand or haven’t made an effort to go and find out if there is some kind of an ordinance in place, it’s probably a good idea to do so,” he says. “If you don’t, you’re going to run into police or an enforcement person who is going to issue a fine or a ticket. So, it’s better to know upfront that you’re in compliance.”
Go electric
Switching from gas-powered to quieter-running, pro-grade battery mowing and maintenance equipment is a prudent option landscape pros can consider when troubleshooting local ordinances.
Roswell, Ga.,-based Ed Castro Landscape serves the greater Atlanta region, and has begun the conversion to battery-powered landscape equipment to meet client preferences for reduced noise and emissions. Ed Castro Landscape is a full-service landscape company whose service offering is 55 percent landscape maintenance (mowing and turf care, enhancements, irrigation, tree work, etc.) and 45 percent design-build landscape construction, serving a client portfolio that is 30 percent residential and 70 percent commercial.
“Currently, we’re undergoing that transition, and we have a number of clients who are with us because we offer battery-powered services,” says Aaron Vilchez, director of maintenance.
“And as this technology grows, we’ll be able to offer more of this service to clients concerned about noise and emission pollution.”
However, the cost of large-scale conversion — particularly the price of lithium-ion batteries — isn’t financially feasible for all landscape companies, especially small to mid-sized outfits operating on tight margins.
Landscape contractors must budget properly for this transition, and Vilchez advises treating battery-powered equipment as a capital expenditure to spread costs over time. In addition, he suggests increasing maintenance rates to recoup the investment because clients are often willing to pay more for the benefits of battery-powered equipment.
Send the correct message
Whether proactive or reactive, landscape pros must build goodwill correctly and transparently with their clients about noise and equipment issues.
Landscape pros must correctly train their crew to react and manage a situation where someone complains directly about equipment issues. Mann suggests teaching crews the art of being good, sympathetic listeners who acknowledge the complainant’s frustration and suggest they contact their boss or owner to discuss the issue further.
“Often, people just want their concerns to be heard by someone,” Mann says. “After they vent, it’s often enough to diffuse the situation.”
Likewise, a proactive and transparent communication strategy can effectively address a landscape contractor’s regulatory challenges. Mann suggests educating customers about the indispensable role of their current equipment lineup and the lack of viable alternatives. In addition, try to reach a sympathetic ear with those who oppose landscape work. Remind people that you’re a local business owner, that your company employs people from the community and that you’re a vital part of the local economy.
Alter practices
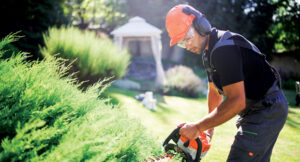
Twenty-plus-year landscape industry veteran Tom Smith says doing business in the Phoenix market creates significant logistical challenges. In his market, a contractor more often runs afoul of local daylight-hour ordinances rather than direct noise violations, even though noise is what generates most complaints.
During a Phoenix summer, it’s not uncommon for daytime temperatures to top out at 110 degrees F, says the owner of Desert Designer Landscape and Development, which focuses 100 percent on landscape design-build work. The searing midday temperature forces Smith’s crews to start their workday at an early hour to be more productive. However, this can generate complaints from nearby residents who are angered at the noise too early or too late in the day.
“If I don’t get started early, then there’s a good chance I’m sending someone to the hospital by noon,” Smith says.
To troubleshoot this problem, Smith has begun rotating elements of a project. Aspects that call for equipment to run are held off until later in the day when the noise is less impactful to nearby residents. Manual or hand labor is focused on during the day’s cooler hours. Most importantly, to keep the workflow going, Smith strategizes and plans the evening before on the types of less intrusive work to complete the next morning.
“Yes, this adds time to a project’s schedule, but it allows us to work while keeping my people safe and the neighbors nearby from logging a complaint,” Smith says. “The extra margins gained from a shorter project turnaround aren’t worth sending someone to the hospital in an ambulance for heat stroke.”
Exercise common sense
Many landscape pros operate in densely populated areas with residential homes close together. The persistent din of leaf blowers, edgers, trimmers and mowers creates a pervasive noise environment, especially during prolonged fall and spring clean-up activities.
The landscape industry bears a degree of responsibility for exacerbating this issue, Mann says. To illustrate this point, Mann offers a striking example he observed firsthand — a landscaping crew deployed nine backpack blowers simultaneously on a single landscape during an April cleanup at a hospital. The combined noise output exceeded the decibel level of ambulance sirens within the hospital zone.
“Landscape pros need to use a modicum of tact about using this equipment,” Mann says. “You don’t need to have nine people standing next to each other blowing in a line. This just drives complaints and makes people mad.”