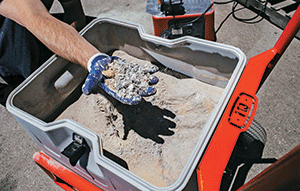
Landscape contractors who work with hardscape materials are taking note of the Occupational Safety and Health Administration (OSHA) Respirable Crystalline Silica standard, which affects the type of equipment and practices they use on the job site.
Crystalline silica is a mineral found in materials like stone, concrete, brick, sand and mortar. Respirable particles are created from the crystalline silica when workers cut, drill, crush or grind these materials.
The particles can get into workers’ lungs and cause an incurable and sometimes deadly lung disease called silicosis, as well as lung cancer, other respiratory diseases and kidney disease. More than 200 workers die each year from silicosis, according to the National Association of Landscape Professionals (NALP).
To limit workers’ exposure, OSHA passed two new standards—one for construction and the other for general industry and maritime—that reduce the permissible exposure limit for respirable crystalline silica to 50 micrograms per cubic meter of air, averaged during an eight-hour day. Construction employers (including landscape contractors) were required to comply by Sept. 23, 2017.
The standard includes implementing an exposure control plan for projects with crystalline silica, training employees to safely work around silica and keeping records of the compliance practices. See the sidebar on page 41 for more details.
Here’s a look at what industry experts are saying about the new standards and what landscape business owners can do to comply.
Industry impact
The three experts we interviewed agree that the new silica standard is good for the industry because it helps create safer work environments. However, that doesn’t come without extra effort and resources.
“This new standard may be a bitter pill for some to swallow now due to new equipment costs and added safety protocols,” says Sarah Hurtado, marketing communications manager for iQ Power Tools. “But it will be very beneficial in the future by improving the health of contractors and will increase the longevity of their careers.”
Landscapers who work with affected hardscape materials, such as Caleb Auman, owner of Auman Landscape, are making the changes a daily part of their job site routines to protect their companies and, most importantly, their employees.
“It’s something you know that’s terrible for you and can get in your lungs,” Auman says. “The more I’ve read, it really drives home the fact that it’s serious.”
He encourages others in the industry to educate themselves on what silica is, what the rules are, what the standards apply to and exposure limits.
“Inform yourself what’s actually at stake and what you need to do,” Auman says. Auman’s customers are 90 percent residential and 10 percent commercial, and they primarily focus on design/build projects—especially hardscapes. Located in Lancaster, Ohio, the firm has an annual revenue of $500,000.
“We’ve always known silica dust isn’t good for you,” Auman says. “We tried to limit exposure to it in the past. Since the rules have come out, we’re more adamant about cutting wet to control the dust.”
He bought specialized cutting saws this year to capture dust, along with personal protective equipment masks.
“Always buy the best equipment you can afford at the time,” Auman says. “Maybe start with dust masks and cutting wet and then go to dust-capturing equipment—or do what you need to do to get in compliance.”
In addition to wet saw technology and wearing a respirator, Sam Steel, NALP safety adviser, says landscapers need to instruct crew members to remove excess dust with a vacuum (instead of blowing a site clean), add a warning barrier around the immediate area, shower and change clothes before going home (if possible), see a doctor if they’ve been exposed to silica and refrain from eating, drinking or smoking in the exposure area.
The National Institute for Occupational Safety and Health provides recommendations for the type of respirators employers should use.
Preparation is key
It’s critical for owners to train their teams and educate new employees as they are hired during the year, Steel says. The employer is responsible if the workers aren’t using the proper tools and practices. “The training needs to be done before the workers are exposed to the hazards,” Steel adds.
Landscapers must document training efforts, including the title of the training, the date it was done and which employees were present, and then have everyone who was present sign a document saying they participated.
“OSHA will want to know that (information) if they come to do a visit,” Steel says. “If you aren’t doing the training under the new standard, that’s a serious violation. Training is very critical.”
Owners also need to create their exposure control plan, Steel says, which should include items like their methods on how to protect workers from silica dust; which saws and grinders are being used; if they’re using wet saw technology or dust-control equipment; the water supply around the cutting or grinding wheels; available respirators; and any other steps taken to protect workers.
“Be smart about your health and job site,” Hurtado says. “Staying in compliance is going to keep you and your team healthier, increase your efficiency and, ultimately, grow your business.”
It isn’t only landscapers who are taking steps to encourage compliance. Many tool manufacturers are also working to create add-ons such as vacuum hoses to their existing tools, Hurtado says. For example, iQ Power Tools offers tools with an integrated vacuum system, filter system and dust containment.
Manufacturers should also provide safety data sheets if their products contain silica, including information on how to safely handle hazardous components, health concerns associated with the materials and any other specific instructions, Steel says.
Cost of noncompliance
Of course, these changes come at a cost. OSHA predicts the new standard will result in an annual cost of about $1,242 for the average affected workplace, with the cost being around $550 for companies with fewer than 20 employees.
Beyond the equipment, there’s also the direct cost of additional labor involved with complying, Auman says. Crews have to spend more time cleaning up any slurry produced by wet cutting, for example.
“Yes, there is a cost upfront, but it is viewed more as an investment,” Hurtado says. “These contractors are improving their respective workforces, as well, by simply keeping their teams healthy.”
However, the cost to comply doesn’t compare to what companies can face in penalties from OSHA if they are noncompliant. Each serious violation results in a nearly $13,000 fine. After a serious violation, they can face a willful violation if they don’t comply, and those fines are about $130,000 per violation.
“The first infraction could cause enough fine money to be the equivalent of some contractors’ annual net profits and the second, that of an entire business by not following the new silica regulations,” Hurtado says.
The bottom line is that these standards were put in place to protect workers’ health now and in the
future—something the entire industry can get behind.
“Regulation or not, no one should be breathing in this harmful silica dust,” Hurtado says. “There are options and solutions to becoming compliant and reducing the dust on your job site.”
How to comply
There are six requirements employers must meet to comply with the new crystalline silica standards, according to OSHA:
- Establish and implement a written exposure control plan.
- Appoint someone to implement the written plan.
- Restrict housekeeping practices that expose employees to silica where other alternatives are available.
- Offer medical exams every three years for workers who are required by the standards to wear a respirator for 30 or more days a year.
- Train crew members on projects that result in silica exposure.
- Record exposure measurements, objective data and medical exams.
For more details, visit OSHA.gov/dsg/topics/silicacrystalline.