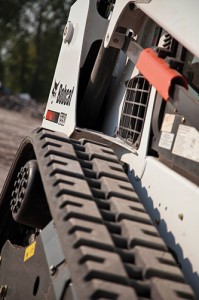
With a surge of interest in rubber tracks for compact construction equipment, tracks and tire manufacturer McLaren Industries offered a dozen pointers for prolonging rubber track life.
They are as follows.
1. Maintain the undercarriage
If undercarriage parts are starting to wear out, replace them promptly. Worn sprocket teeth can pull out the links from tracks, and worn rollers can cut the rolling area of the track, causing serious damage. It’s important to use a pressure washer to clean the undercarriage. Neglecting to wash it can cause the recoil mechanisms to fail and, in turn, the track cables to break.
2. Avoid too much tension
Always refer to the manufacturer manual for the proper tension, as different size machines require different tensions, and check the track tension each week. While some people believe keeping track tension especially tight will make it last longer, that’s not the case. Some flex is needed, or the track will react similarly to an overinflated tire. Conversely, too loose tracks eventually can damage the cleats around the planetary drive wheel.
3. Stay on track
De-tracking can cause catastrophic damage to rubber tracks, with the severity correlating with the length of time the operator continued to use the machine. While an experienced operator can recover a partially de-tracked machine with a series of maneuvers, a completely de-tracked machine will need to be moved to a stable, level area for the tracks to be repositioned.
4. Don’t cruise over curbs
Driving over curbs puts excessive stress on tracks, which can cause de-tracking. If the tracks stay in place, the stress could cause the rubber to crack. It’s a domino effect from there: Chunks of rubber fall off, exposing internal steel cords to moisture, which leads to corrosion and, ultimately, track failure.
5. Drive carefully
Remember that while tracks will not puncture like pneumatic tires, sharp objects still should be avoided. Jagged debris can cause rubber pieces to slice off, reducing the track’s effectiveness and eventually damaging the inner steel cords. When it comes to aggressive terrain, steel tracks may be a better option.
6. Avoid contaminants
Chemicals, oil, salt and farmyard manure, as well as other abrasive environments, can wreak havoc on a set of tracks, causing the rubber to deteriorate. Avoid these elements if at all possible. Also, keep an eye out for hydraulic oil and grease that may drip from the machine onto the tracks. If the tracks do become exposed to any of these elements, rinse them immediately afterward.
7. Check sizes
Ensure that the track size matches the machine’s hp. If there is more hp than track tension, slippage—and subsequent wear damage—will occur.
8. Keep looking forward
Traveling in reverse, especially at high speeds, will unnecessarily stress the tracks, which are designed for forward motion. Putting a notice on the dashboard may help remind operators of this.
9. Rotate regularly
Rubber tracks should be rotated periodically to ensure even tread wear. When it’s time to replace the tracks, do both at the same time. Replacing only one track at a time may cause alignment issues and damage the undercarriage.
10. Take it easy
No matter the type of undercarriage, rubber tracks will wear with prolonged use. Limiting travel, when possible, will minimize this wear. Additionally, avoid driving across slopes and making fast, sharp turns, which may speed up the wear process.
11. Avoid direct sunlight
When the machine is parked for the long periods of time, make sure it’s in the shade, or cover the tracks with tarp or cloth. Sunlight is a natural enemy of any rubber product, including rubber tracks. This preventive action alone can double the track life.
12. Store tracks properly
When the tracks are not in use, store them in a cool dry environment, and allow them to rest on their sides in a relaxed position to prevent crimps and folds. If the tracks are left on the machine, operate the vehicle at least once every two weeks for about five minutes to help maintain track flexibility and prevent the tracks from becoming misshapen.